Bearing issue detection
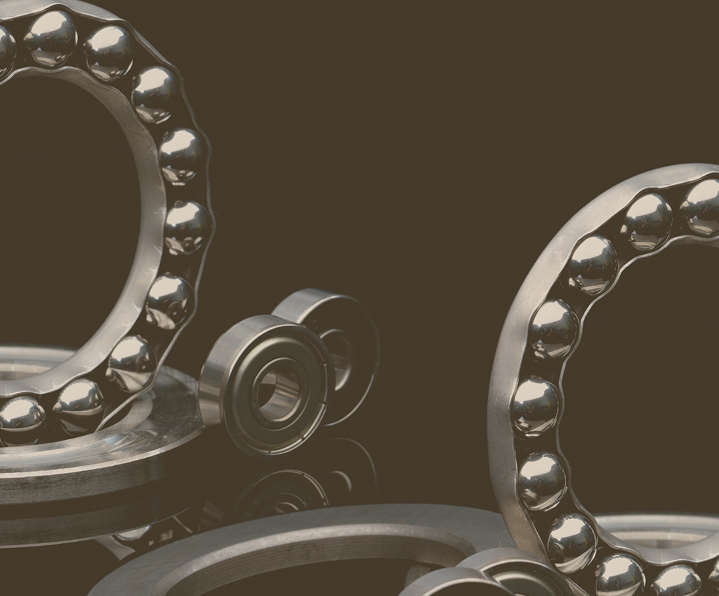
Abnormal vibrations patterns
During months into the autonomous IoT trial, analytics detected abnormal vibration patterns that progressively worsened with each day.
Alerting the customer
Alert was promptly shared with the wagon owner, enabling planned maintenance to be scheduled two weeks later.
Next steps
The bearing was successfully replaced, ensuring the timely delivery of critical components, avoiding downtime and preventing a potential catastrophic derailment
What has happened?
Upon bearing disassembly a defect was found. Damage accumulated by the outer bearing raceway, ~15mm in size measuring along the short axis. This deterioration was rapid, not the kind that unfolds over several years. The bearing defect was a consequence of inadequate sealing, resulting in lubricant leakage.
Full timeline
Week 1 – First vibration patterns
Week 2 – Alert & maintenance scheduled
Week 3 – Components order
Week 4 – Depot visit & bearing change -> wagon immediately back to work
Savings
- Without Powerail, emergency repairs and downtime could cost €20,000 per incident.
- With Powerail, proactive detection reduced costs to €300, as repairs were aligned with scheduled maintenance.
- Prevented significant fines and operational disruptions.