Early detection of wheel defects
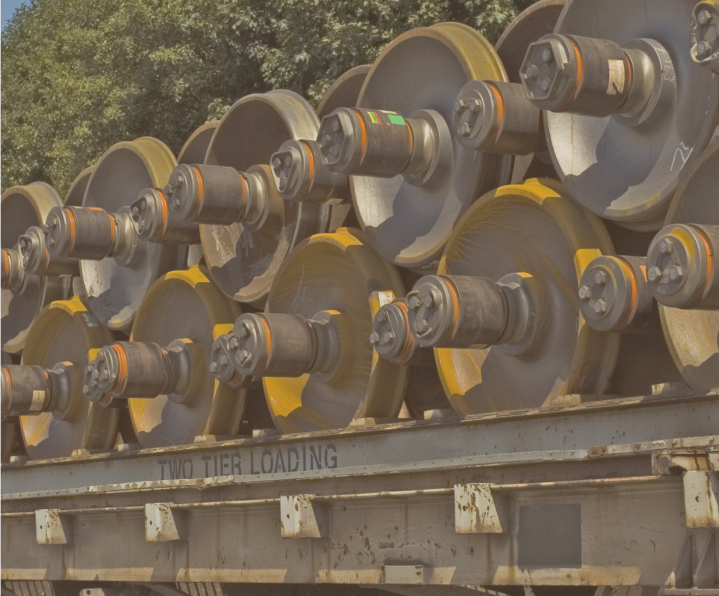
Abnormal vibration patterns
In the first month of the trial, Powerail detected abnormal vibration patterns – recurring periodic shocks in the data, which is a strong indicator of wheel surface defects such as flat spots.
Alerting the customer
Once the flat spot pattern was confirmed, an alert was promptly shared with the wagon owner. This enabled early planning and rerouting to an internal maintenance depot.
Next steps
The wheel was reprofiled at the operator’s internal facility during scheduled maintenance, eliminating the need for urgent third-party repairs or unexpected downtime.
What has happened?
Upon inspection, a 30 mm flat spot was identified on one of the wagon wheels. The most likely cause was a wheel lock-up during braking — potentially due to uneven brake force distribution or sudden emergency braking.
Such incidents often go unnoticed in daily operations, especially if manual inspections are limited. Over time, even a moderate flat spot like this one can grow larger, increasing wear on suspension components and reducing wheel lifespan.
If left undetected, the defect would have worsened, potentially requiring full wheelset replacement and risking further damage to the wagon or surrounding infrastructure.
Full timeline
Day 1 – Wheel defect data collected and pattern confirmed
Day 2 – Alert sent & maintenance scheduled
Day 3 – Rerouted wagon to depot & wheel reprofiled
Day 4 – Wagon returned to normal operation
Savings
Proactive detection enabled simple reprofiling during scheduled maintenance, avoiding a potential emergency repair of up to €7,500 per incident and 3 – 5 days of downtime. Estimated savings: €1,000 – €6,300 per wagon.